Perspectives on Chip Loading
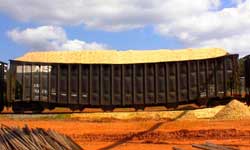
Most mill managers only dream about having the "problem" of overloading their chip cars. But certain shippers in Alabama, Arkansas, Georgia, Mississippi and North Carolina DO face this issue. One chip mill accidentally sent a car to the mill 18 tons overweight, while a different mill unintentionally sent a car 18½ tons overweight!
Chip car gross weights seem to fall into three general categories:
- 286,000 lbs.: The majority of cars seem to have this rating. Payloads range from 95-100 tons for bottom-dump cars. Rollover car payloads range from 98-107 tons.
- 263,000 lbs.: This includes older cars with nominal payloads in the 90 ton range. Many of these cars are being fitted with heavier running gear, converting them to nominal 100 ton capacity.
- 220,000 lbs.: Even older vintage cars, but there are many of these cars still in service. They have payloads in the 75-ton range.
Differing payloads for identical cars result from repairs that decrease the payload by the weight of the repair material. Just like over-the-road trucks, railroad Gross Car Weight is based on a maximum axle/truck load-bearing weight.
A solid cubic-foot of wood weighs 50-60 lbs., depending on specie and water content. A typical cubic-foot of pulp mill quality chips will weigh 22-24 lbs, meaning that this cubic-foot of chips is 56-60 percent air-space. Load-density gains of chips in train cars (or barges) of 25-33 percent represent displacing just one-third to one-half of that air volume between those chips!
Here is how this works with chip cars:
A chip car loaded with solid wood will be only about half filled. For a chip car to be loaded, tonnage-wise, with free-fall chips, it would have to be filled to 115 percent of full, obviously an impossibility. Getting one-third of the air out of the free-fall loaded chips gives a full payload of chips with the car only 90 percent filled.
How to Balance Car Loading
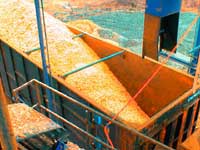
Here, a belt-scale "tripped" the car-mover to pull this older car when the 90-ton rated payload was reached. That left a gap on the back-end of the car, meaning the front-end was overweight!
Furthermore, because of the distance from the end of the car, when the scale "tripped," 2-3 more tons got loaded before the puller could move an empty car under the loading chute!
But, the overriding question is this: In this era of ever-increasing freight rates, how is it possible for a chip car to be overloaded in the first place?
Technology does exist for increasing chip car payloads. The "Techniques", "Whirley Wizard", and "Chip Flinger" pages identify and explain six payload-enhancing methods. As one might expect, efficiency of these devices ranges from "uncertain" to "impressive."
So why seek 100% payloads?
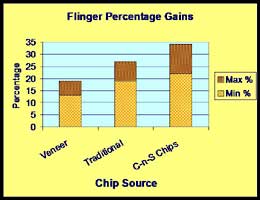
At a recent Papricon meeting in Vancouver, the keynote speaker stated that 30 percent of overall paper-production cost is transportation. Utilizing any and all means to maximize rail payloads is a step towards taking a very noticeable chunk out of that cost-component!
- If only 11% MORE chips are loaded into nine cars, the chips for a 10th car have already been included in the previous nine cars. Therefore, that tenth car freight is FREE!
- If only 15.4% MORE chips are loaded into 13 cars, the 14th and 15th car freight is similarly FREE!
Increase Chip Shipment
Mills with limited rail space or restricted chip-car availability can now produce additional (bonus) chips on the same number of cars, which for some mills overshadows the transportation savings from full payload chip cars!